By Ma Ruishan, People's Daily
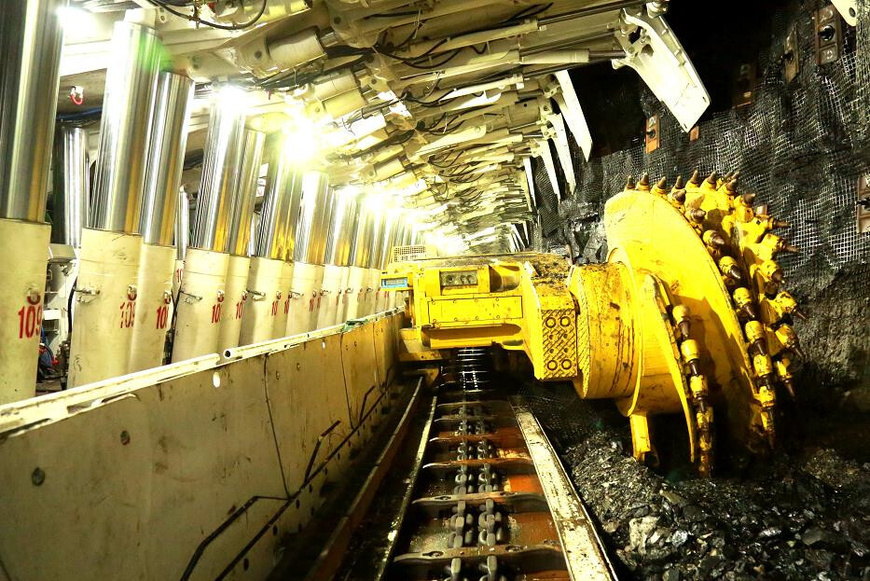
Photo shows an intelligent work face of the Tashan Mine in north China's Shanxi province. (Photo provided by Jinneng Holding Group)
At the Malan Mine in Taiyuan, north China's Shanxi province, a group of new "workers" has just reported for duty. But instead of helmets and headlamps, these workers come equipped with sensors, software and precision memory-cutting technology.
Managed by XiShan Coal Electricity Group Co., Ltd. (XiShan Group), a subsidiary of Shanxi Coking Coal Group Co., Ltd., the mine now runs with the help of an intelligent control center above ground. Here, Ding Chao, deputy technical leader of the mining preparation team, sat in front of a smart mining console. With a tap of a button, he set an automated shearer in motion more than 100 meters below. Its rotating drums sliced cleanly into the coal seam, sending streams of freshly hewn coal - known locally as "black gold" - onto a conveyor belt bound for the surface.
Live footage from underground work zones flickers across monitoring systems. Hao Yirui, head of the coal mining section, watched closely. "If the belt drifts even slightly off track, we can notify workers immediately," he explained.
The scene is emblematic of a broader transformation underway in Shanxi, China's largest coal-producing region. As smart mining continues to expand, technologies like intelligent mining systems and robotic inspectors are becoming indispensable partners underground, working in coordination with human operators.
How does technology coordinate with human labor?
Central to this shift is the smart mining system - a digital "brain" that integrates control, coordination, and diagnostics across the mine. Once-manual tasks have been translated into automated commands. Workers now guide machines remotely, relying on pre-programmed "memory-cutting" paths that reduce manual labor and boost mining efficiency.
Smart technology also plays the role of "safety supervisor."
At the nearby Tunlan Mine, also managed by XiShan Group, an AI-powered early warning system adds a layer of vigilance. At 2:55 a.m., one recent night, Wang Jianping, a member of the electromechanical maintenance team, received an alert on his phone: a fan in the equipment room had malfunctioned. Technicians were dispatched immediately, the fault repaired within minutes.
The platform monitors not only machines but also human activity, issuing alerts to workers when potential hazards are detected. It is, in effect, an always-on safety supervisor.
Roof collapses - among the most feared threats in coal mining - remain a critical concern. Traditionally, installing hydraulic shields to hold up the roof above the work face was a labor-intensive and risky task - often requiring two workers and leaving them exposed to falling rocks. Now, equipped with infrared sensors, the shields advance automatically, extending their hydraulic arms to stabilize the coal wall without putting workers at risk.
"In the past, we needed over a dozen workers at a single face and still couldn't keep up," said Hao. "Now we run day shifts only, with a team of only eight. Output hasn't dropped - in fact, we've improved productivity by over 40 percent."
After extraction, how is the coal safely delivered to the processing plant?
Even after the coal is brought to the surface, the technology continues to work. At the Malan Mine, raw coal travels down a steep 1,142-meter incline toward the processing plant. Along the way, a smart inspection robot glides along the belt, scanning for signs of trouble.
Its data-gathering cameras can track belt alignment and coal spillage. The built-in pickup microphones record and analyze mechanical sounds to detect anomalies and trigger automatic alarms if anything seems off. An infrared thermal imaging camera "feels" for abnormal heat in hard-to-reach areas, alerting workers to potential issues before they escalate.
"It's like giving the robot human senses," said Guo Tianjun, chief engineer of the Malan Mine's electromechanical department. "It sees, hears, and feels, eliminating inspection blind spots and easing the burden on workers. It's reliable."
To date, the Malan and Tunlan Mines have jointly built 16 smart mining work faces. Across Shanxi, more than 50 percent of coal production capacity comes from mines powered by intelligent systems.
"With continued upgrades in rock-coal recognition and underground positioning technologies, fully unmanned mining is no longer a distant vision - it's just around the corner," said Hao.
Managed by XiShan Coal Electricity Group Co., Ltd. (XiShan Group), a subsidiary of Shanxi Coking Coal Group Co., Ltd., the mine now runs with the help of an intelligent control center above ground. Here, Ding Chao, deputy technical leader of the mining preparation team, sat in front of a smart mining console. With a tap of a button, he set an automated shearer in motion more than 100 meters below. Its rotating drums sliced cleanly into the coal seam, sending streams of freshly hewn coal - known locally as "black gold" - onto a conveyor belt bound for the surface.
Live footage from underground work zones flickers across monitoring systems. Hao Yirui, head of the coal mining section, watched closely. "If the belt drifts even slightly off track, we can notify workers immediately," he explained.
The scene is emblematic of a broader transformation underway in Shanxi, China's largest coal-producing region. As smart mining continues to expand, technologies like intelligent mining systems and robotic inspectors are becoming indispensable partners underground, working in coordination with human operators.
How does technology coordinate with human labor?
Central to this shift is the smart mining system - a digital "brain" that integrates control, coordination, and diagnostics across the mine. Once-manual tasks have been translated into automated commands. Workers now guide machines remotely, relying on pre-programmed "memory-cutting" paths that reduce manual labor and boost mining efficiency.
Smart technology also plays the role of "safety supervisor."
At the nearby Tunlan Mine, also managed by XiShan Group, an AI-powered early warning system adds a layer of vigilance. At 2:55 a.m., one recent night, Wang Jianping, a member of the electromechanical maintenance team, received an alert on his phone: a fan in the equipment room had malfunctioned. Technicians were dispatched immediately, the fault repaired within minutes.
The platform monitors not only machines but also human activity, issuing alerts to workers when potential hazards are detected. It is, in effect, an always-on safety supervisor.
Roof collapses - among the most feared threats in coal mining - remain a critical concern. Traditionally, installing hydraulic shields to hold up the roof above the work face was a labor-intensive and risky task - often requiring two workers and leaving them exposed to falling rocks. Now, equipped with infrared sensors, the shields advance automatically, extending their hydraulic arms to stabilize the coal wall without putting workers at risk.
"In the past, we needed over a dozen workers at a single face and still couldn't keep up," said Hao. "Now we run day shifts only, with a team of only eight. Output hasn't dropped - in fact, we've improved productivity by over 40 percent."
After extraction, how is the coal safely delivered to the processing plant?
Even after the coal is brought to the surface, the technology continues to work. At the Malan Mine, raw coal travels down a steep 1,142-meter incline toward the processing plant. Along the way, a smart inspection robot glides along the belt, scanning for signs of trouble.
Its data-gathering cameras can track belt alignment and coal spillage. The built-in pickup microphones record and analyze mechanical sounds to detect anomalies and trigger automatic alarms if anything seems off. An infrared thermal imaging camera "feels" for abnormal heat in hard-to-reach areas, alerting workers to potential issues before they escalate.
"It's like giving the robot human senses," said Guo Tianjun, chief engineer of the Malan Mine's electromechanical department. "It sees, hears, and feels, eliminating inspection blind spots and easing the burden on workers. It's reliable."
To date, the Malan and Tunlan Mines have jointly built 16 smart mining work faces. Across Shanxi, more than 50 percent of coal production capacity comes from mines powered by intelligent systems.
"With continued upgrades in rock-coal recognition and underground positioning technologies, fully unmanned mining is no longer a distant vision - it's just around the corner," said Hao.